Case Studies
Transforming Businesses with Innovative ServiceNow Solutions
Automation of Make-to-Order (MTO) Process Using ServiceNow FSM Module
The Make-to-Order (MTO) Work Order process is enhanced with ServiceNow’s FSM module, integrating with ERP systems to provide real-time access to BoM data, inventory, and parts details, ensuring greater accuracy and efficiency.
Overview
The Make-to-Order (MTO) Work Order process is streamlined by automating creation, assignment, tracking, and closure within the Field Service Management (FSM) module of ServiceNow. Integration with ERP systems ensures real-time access to Bill of Materials (BoM) data, inventory status, and parts details. Configure workflows and business rules optimize resource allocation by assigning tasks based on technician availability, skills, and location. Automated notifications keep stakeholders informed, while dashboards provide real-time visibility into work progress. This automation enhances accuracy, reduces turnaround time, and improves overall service delivery.
Background
Technology
ServiceNow FSM Module
ServiceNow Integration Hub
High level Process
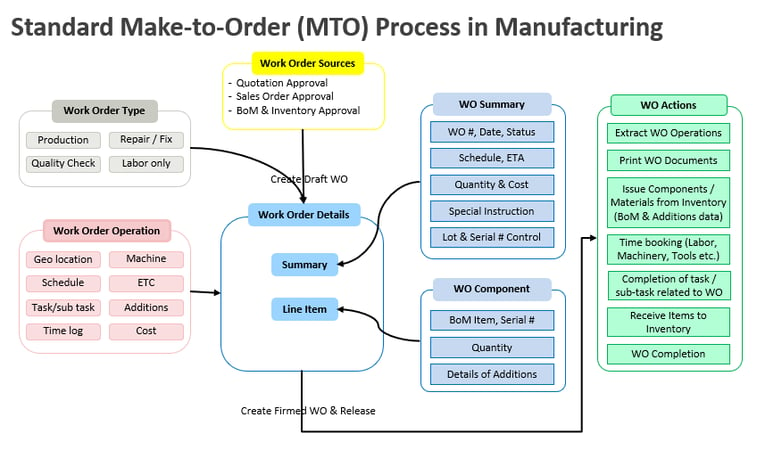
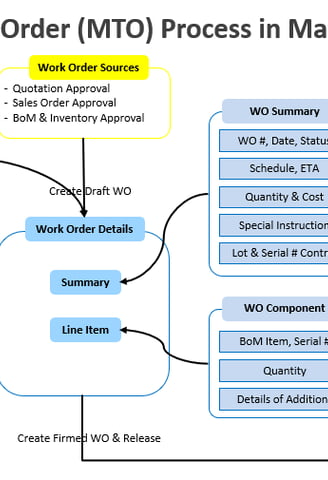
A Work Order (WO) is an official directive for manufacturing to produce, refurbish, or rework an item. It enables the efficient consumption of materials, labor, machinery, and overhead costs throughout the production process. Work Orders provide essential information to various departments for effective planning, scheduling, and shop floor management. Additionally, they serve as a central record for tracking both standard and actual costs.
The Make-to-Order (MTO) approach ensures that products are only manufactured after a customer places an order, enabling customization and reducing inventory costs.
Key Objectives & Requirements
Work Order serves as authorization for manufacturing to use resources (materials, machinery, tools, labor, etc.).
Plan and schedule work assignments to Work Centers and machines.
Optimize the utilization of all resources for maximum efficiency.
Assist Work Centers in work and capacity planning.
Maintain a permanent record of actual materials issued and received upon Work Order completion.
Capture cost details, including materials, labor time, and machine time.
Provide real-time visibility into work status and generate analytics reports.
Ensure easy traceability using serial and lot numbers.
Solution Implementation
1. ServiceNow Integration with External Applications via Integration Hub
Quotation Management Application: Retrieves real-time status of quotations and buyer-specific requests.
Sales Management Application: Tracks Sales Order status, packing, labeling, and delivery details.
ERP System: Fetches BoM data for required parts or materials to complete the Work Order.
Inventory Management / ERP System: Checks real-time inventory status, facilitates material issuance, and updates inventory upon Work Order completion.
2. Work Order Management & Execution
Creation and management of tasks/sub-tasks within WO including quality check related sub-task.
Assignment to relevant teams based on business rules and validations.
Scheduling tasks based on capacity and availability of machinery and tools.
Resource allocation based on technician availability, skills, and location.
Work Order Printing: Generate PDF formatted WO using custom report generation functionality.
3. Cost Analysis and Audit log
Cost calculation: Capture actual resource utilization, including materials consumed, additions consumed, labor hours, and machine time.
Tracking tracing: Tracking cost distribution, calculation of margins by WO (contribution margin, gross margin) and other cost analytics.
Electronic Approvals & Audit Logs: Manage approval processes and maintain audit trails.
4. Real-time Monitoring & Performance Tracking
SLA tracking to ensure timely execution.
Dashboards and analytics for insights into work order trends.
Real-time alerts and notifications to keep stakeholders updated.
By leveraging ServiceNow FSM and Integration Hub, the automation of the Make-to-Order Work Order process significantly enhances efficiency, visibility, and cost management. This solution not only optimizes resource utilization but also ensures seamless communication between various systems, ultimately leading to improved customer satisfaction and streamlined operations.
Want to achieve seamless implementation of ServiceNow FSM module, work order process, establish integration with ERP or other application? Contact Praansh Information System today!
Contact us at Info@PraanshInfoSys.com
info@praanshinfosys.com
© 2025. All rights reserved.
Solutions
ServiceNow IT Service Management
ServiceNow IT Operations Management
ServiceNow IT Asset Management
ServiceNow Strategic Portfolio Management
ServiceNow IT Governance, Risk and Compliance
ServiceNow HR Service Delivery
ServiceNow Workspace Service Delivery
ServiceNow Customer Service Management

